Continuous improvement is defined as an ongoing effort to improve all elements of an organization—processes, tools, products, services, etc. Sometimes those improvements are big, often they are small. In this case, “don’t sweat the small stuff,” doesn’t apply. But what’s most important is that all are frequent. Companies that excel at continuous improvement start with the belief that success comes from:
• Innovating “how” they do what they do (big and small).
• Engaging all employees in sharing knowledge and generating improvement ideas.
• Exploring better ways to deliver to customers and respond to changes in the external environment.
Fostering a continuous improvement culture is rooted in three practices:
- Performance transparency starts with making goals public and cascading those goals in a way that is tailored to individuals at all levels of the organization. Progress toward goals must be transparently tracked to give all clear visibility into what is working and what needs work.
- Knowledge sharing is critical to scale best practices across (and up and down) organizations.
- Employee involvement is a necessity in continuous improvement. Frontline employees are closest to the work, and thus typically have the richest insights on how their work can be done better. Capturing their perspectives is critical.
Core to a continuous improvement mindset is the belief that a steady stream of improvements, diligently executed, will have transformational results. Transformational results are key to all business at BioZyme®. In 2020 we worked diligently through an initiative we called the Courage to Change. Change is always hard, and we had many things identified (both big and small) to work toward considering our emphasis on a continuous improvement mindset.
In order to keep us focused we chose to align our improvement initiative with our corporate goal of safe, accurate product. Throughout this month’s VISION, you will be able to read how we have defined this goal and all the things we have invested in to ensure we can deliver on our definition. Behind the scenes, millions of dollars are being spent to ensure statistical process controls are being used to ensure the initiative is alive and well in all that we do. Our equipment investment in proactively addressing (magnet drawers, feed cleaners, sifters, screens and quality inspections) safe and accurate product has been significant over the last few years, and we continue to increase all of our sampling and testing through high precision in-house analyzing with quick turnaround times so that we can ensure product homogeneity bag to bag and quarter to quarter.
Continuous improvement whether big or small is hard. Why? It involves that word we humans do not like – CHANGE. There are three main reasons people hate change — lack (or perceived lack) of reward, fear of the unknown and loss of status or visibility in the organization. Address these concerns head on so continuous improvement is ingrained in your organization.
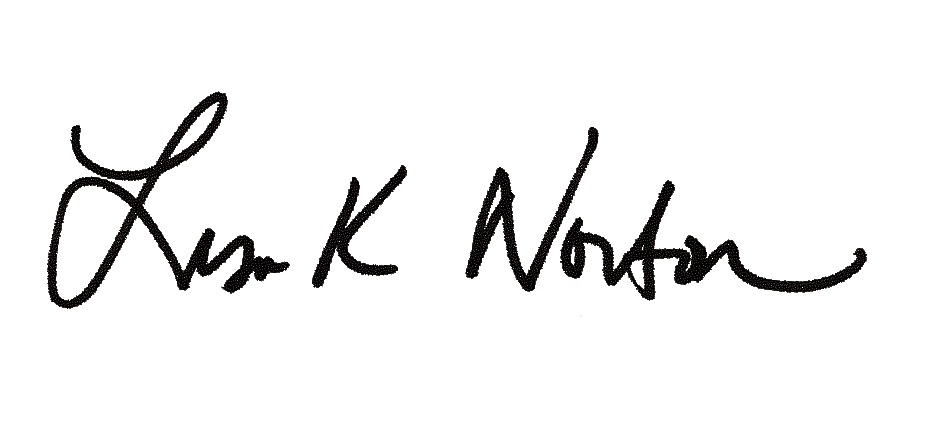