As the last weeks of the year wind down and we make plans for a new year, it is often fun to reflect on the year’s accomplishments. 2024 has definitely been a busy and successful year at BioZyme®, and we have much to be grateful for.
Let’s stroll down memory lane to reflect on some of the exciting new products and partnerships that this year has brought to our team.
2024 Brings New Products, Exciting Collaborations
A business simply can’t grow if it continues to do the same thing, day after day and year after year. With sales growth and diversification as two of BioZyme’s five goals, our team has been busy launching new products for you to share with customers this year.
Remember, these products are formulated around our research-proven prebiotic, AO-Biotics® Amaferm®. Amaferm is the flagship prebiotic that BioZyme is known for. At BioZyme, we understand that digestion and absorption help all animals stay healthy and perform to their optimum.
Transition Vita Charge® to a Technology
The first thing we did in 2024, from a brand perspective, was transition Vita Charge from its own brand line to a technology. All Vita Charge products either transitioned into the popular VitaFerm® or Sure Champ® lines.
The Vita Charge Technology is comprised of a unique blend of ingredients to help support animal health before, during or after the stress response. Every product with Vita Charge Technology contains an exact amount of B vitamins, vitamin E, potassium, zinc, MOS and Amaferm. In addition, a precisely defined salt-to-sugar ratio was developed and incorporated into the technology to support hydration. This combination provides an undeniable impact to livestock under stress, embodying BioZyme’s overall purpose to provide “care that comes full circle.”
New product names include:
VitaFerm One
On February 1, we introduced the VitaFerm ONE line to the world at the Annual Cattle Industry Convention in Orlando. This “One Solution for All Seasons” mineral initially came as a loose mineral and a 35-pound mineral block. We have also added the following options:
Mid-year, when we added VitaFerm ReproMaxx™, VitaFerm ONE became the first level of mineral in the VitaFerm line’s Good, Better, Best marketing structure we introduced at the Dealer Retreat.
Good: VitaFerm ONE provides one solution to conveniently and consistently promote cattle performance in all seasons.
Better: VitaFerm Concept•Aid® promotes effective, easy breeding when fed at least 60 days pre-calving through 60 days post-breeding.
Best: VitaFerm ReproMaxx provides maximum performance within intensive reproductive systems.
DuraFerm® ONE Sheep
We understand that sheep producers are also looking for a simple year-round solution. That’s why we introduced DuraFerm ONE Sheep. DuraFerm ONE is a free-choice vitamin and mineral supplement for sheep that promotes performance year-round.
This was our only new small ruminant product this year, but we have had several requests for other sheep and goat products, so stay tuned.
VitaFerm® ReproMaxx™
This summer, we were able to announce our first exciting collaboration of 2024, with the launch of VitaFerm ReproMaxx. ReproMaxx is one of few minerals designated as Zinpro® Availa 4 Verified.
VitaFerm ReproMaxx products provide high vitamin and mineral fortification and research-proven components. The new line of products maximizes reproductive success by leveraging the benefits of Amaferm and Zinpro Performance Minerals.
“Zinpro is as committed to research and technology as we are,” said Lisa Norton, BioZyme President and CEO. “This is an exciting time for our company, our dealers and our customers.”
In addition to the traditional formula, we also provide a formula to protect against anaplasmosis:
ReproMaxx provides the “premium” mineral in the VitaFerm Good, Better, Best marketing model. Remember, the difference between the three minerals is the intensity of nutrition. ONE provides great nutrition, Concept•Aid provides better nutrition, and ReproMaxx provides the best nutrition.
Partnership with Four Sixes Ranch™ Leads to Legendary Nutrition™ Product Line
This line combines the best of both brands’ expertise to provide comprehensive nutritional solutions designed to enhance the health and productivity of resilient commercial cattle herds.
“I wanted BioZyme to develop a product that works in the real world, not just on an improved small pasture. It has to work in a big pasture. It has got to work in big country. There are still a lot of places in the United States that have ranches that you can’t drive to every corner. You have to have something that works for that,” said Joe Leathers, General Manager at the Four Sixes Ranch.
From One Legend To Another
“I have worked with BioZyme over the years and operated nine different ranches in five different states. The nutritional needs in every one of those states were different. I saw a need for a tub or a product that would work for normal ranchers in different areas to meet the nutritional needs in all those different states. The partnership we have with BioZyme to develop this product would do just that. Not just smaller ranchers, not just purebred operators, but day-in-day-out ranchers that make a living off the land.”
Those words from Leathers summarize BioZyme’s partnership with the Four Sixes. The legendary ranch has been feeding BioZyme products fueled by Amaferm for years. They know the benefits Amaferm offers their 7,000-head cow herd in big country. They want others to get those same benefits when forage is the primary feed source.
The Four Sixes Ranch has worked with the BioZyme Team for 16+ years to provide their herds with industry-leading nutrition. After all, you don’t become a legend by settling for anything less than the best products on the market. And at BioZyme, our relationship isn’t just a partnership— it’s a shared commitment to excellence. The Four Sixes’ trust in us is what ultimately led to our exciting new product collaboration.
Introducing Four Sixes™ x VitaFerm® Legendary Nutrition Protein Tub
The Four Sixes x VitaFerm Legendary Nutrition Protein Tub is a ranch-tested 20% all-natural protein tub with vitamins and minerals designed to support beef cattle health and productivity when grazing moderate to low-quality forage. Furthermore, it:
- Carefully crafted specifically for the legendary Four Sixes Ranch, Legendary Nutrition is now available for operations of all sizes.
- Provides quality nutrition and industry-leading organic copper and zinc proven to deliver real-world results on the ranch.
- Contains AO-Biotics Amaferm, a prebiotic research-proven to enhance digestibility.
Ranch-Tested
Forage utilization is vital to the ranch, which depends on the grasses to feed all 7,000 cows. Amaferm, the key ingredient in every VitaFerm product, helps cattle get the most out of the forage. Amaferm is a prebiotic research-proven to enhance digestibility and increase the energy available to the animal.
“We’re grass farmers with a cow problem… This tub is another tool in our toolbox to give us the ability to take care of our country. To scatter our cows so we don’t overgraze any one area of our country. So, we don’t beat it out, so invasive species don’t come in, all the while maintaining the health and nutritional needs of our cattle,” Leathers said.
Research-Proven
At BioZyme, research is a core value. It’s been this way for more than 7 decades. Why? Because of our motto: care that comes full circle. We believe that every animal we care for ultimately takes care of us in return. Doing what’s right for our animals, our land and our producers comes back around in the end.
Developed using the latest research in animal nutrition, the Four Sixes x VitaFerm Legendary Nutrition product line provides quality nutrition to deliver real-world results. The flagship protein tub combines essential vitamins, minerals and organic trace minerals that are crucial for the overall health, growth and reproductive performance of cattle.
“The collaboration makes perfect sense for cattle producers across the country and for the two companies, who have been doing business together for a long time. We are so pleased to partner with the Four Sixes on the Legendary Nutrition line,” said John Tucker, BioZyme Large Beef Accounts Manager. “With industry-leading organic trace minerals, 20% protein, and Amaferm, the tub is a great and convenient option for operations of all sizes.”
The American Rancher
A December 16 episode of The American Rancher on RFD-TV featured The Four Sixes and this new ranch-tested, research-proven protein tub. On a beautiful fall day, our team and the Sixes Crew filmed a great episode for you to learn more about their ranch philosophy and why the convenient nutrition of a tub is important to them. Tune in to YouTube to watch this episode of The American Rancher.
“The thing about the tub is it’s a complete package. The nutritional needs of the cows shift throughout the year. This is a product you can put out year-round. It will regulate itself. We’ve seen it regulate itself. Therefore, you have a comfort level that is economically feasible. The cows will consume when they need it and won’t when they don’t,” Leathers said.
BioZyme® Earns AFIA Feed Facility of the Year Honor
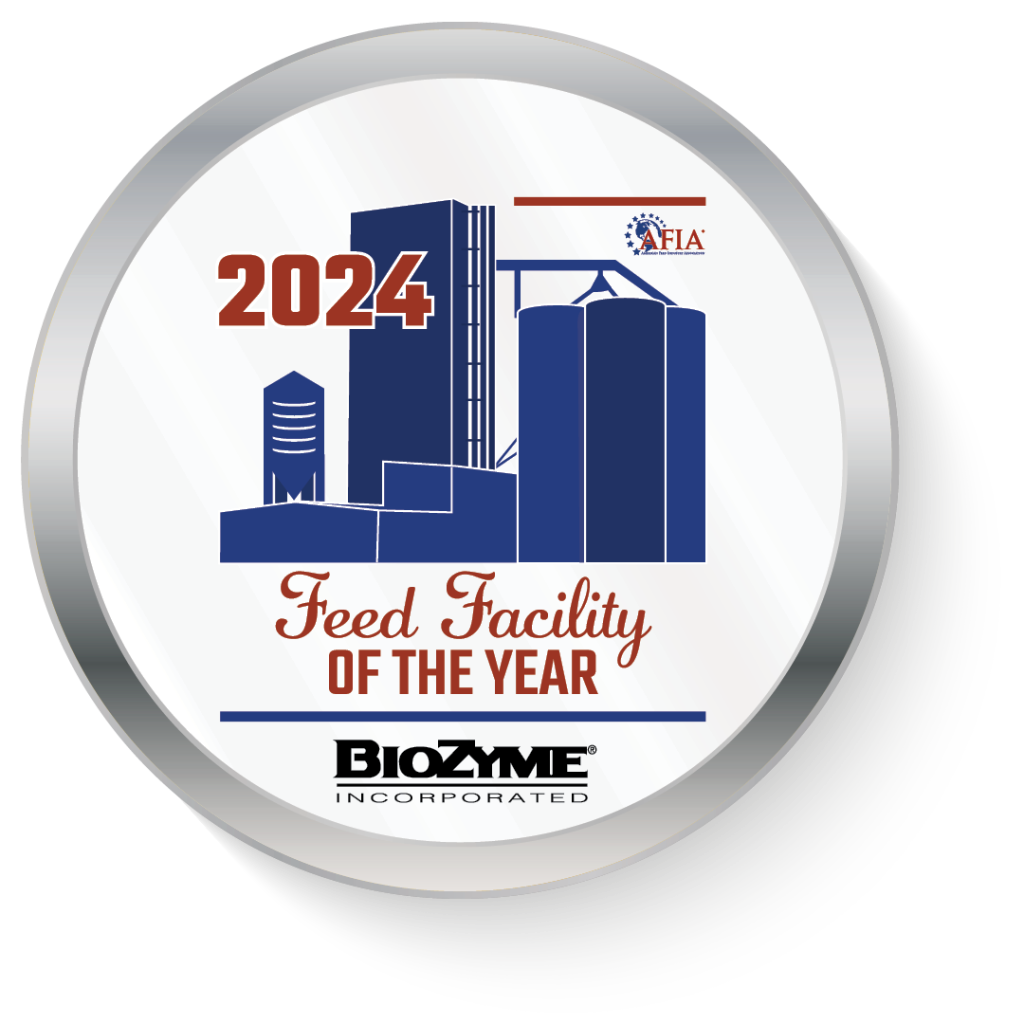
New products and collaborations are exhilarating. However, the most exciting announcement of the year was that BioZyme’s Stockyards location earned the American Feed Industry Association (AFIA) and Feedstuffs 2024 Feed Facility of the Year.
This prestigious award is presented annually to a feed facility demonstrating an outstanding commitment to quality, safety, productivity, regulatory compliance, employee development and customer relations. Additionally, BioZyme received the highest productivity and efficiency score.
BioZyme hosted a special event with employees, customers and special guests on October 31 to celebrate the achievement.
“I am very proud of our team’s shift to a data-minded, continuously improving production facility. We make continuous improvement for our customers a priority every single day,” said BioZyme president and CEO Lisa Norton.
This has been more than a decade-long goal of Norton. She said AFIA positioned the program as a recognition as well as a benchmarking opportunity to enhance continuous improvement.
“We put in a lot of effort through the pandemic and over the last several years to change our culture and data use to be considered,” she said.
A Point of Pride
One of the items that Norton is most proud of is that the entire production team is PCQI (preventative control qualified individual) certified. Although the requirements are that one team member receives this certification, the BioZyme leadership ensured everyone on the production team received certification. The team certification helps ensure the production of safe, accurate product that moves through the plant daily.
“It is such an honor to be a part of this team! We hear all of the time how impressed visitors are with the cleanliness of our facilities. This award means so much more . . . In addition to cleanliness, this award encompasses our commitment to quality. This is only achievable with the quality culture we have created with all of our employees. It’s an honor to work with a team that makes every effort to achieve ‘Care that comes full circle.’ If we didn’t have this team, we wouldn’t be able to achieve this award,” said Robert Cortez, Director of Quality.
BioZyme, an animal nutrition and fermentation company, has been driving innovation since 1951. Founded by Larry Ehlert, BioZyme began as Ehlert’s Guaranteed Feeds with just a $2,500 loan and a small feed store in the St. Joseph Stockyards.
Today, BioZyme’s product line includes high-quality vitamin, mineral and protein supplements enhanced with AO-Biotics® Amaferm®, a prebiotic. The Stockyards plant produces 31,000 tons of supplements annually.
Nationally Recognized
“We were extremely impressed with the BioZyme Stockyards facility, as it is evident that the company and its staff exemplify the core values of the Feed Facility of the Year program,” said Gary Huddleston, AFIA’s director of feed manufacturing and regulatory affairs. “The plant is a shining example of manufacturing excellence in the animal food industry.”
The lengthy application of nearly 180 questions gave employees the opportunity to increase their already high standards in areas such as occupational and safety hazards, sustainability, and utility usage, according to Jill Vanover, Vice President of Quality and Regulatory. She recalls a previous FAMI-QS auditor commenting on BioZyme’s commitment to quality from the top down and noted it as the best he had ever seen.
“This award is possible because of the tremendous pride that all our employees demonstrate throughout the company. They have a love for animals, a belief in the products and understand the importance in the roles they are playing to make safe, accurate products,” Vanover said.
Looking Ahead to 2025
As we reflect on 2024, we can’t help but be a little nostalgic. A lot of WOWing things happened to BioZyme. But the windshield is larger than the review mirror for a reason. We look forward with great anticipation and know that 2025 will also bring new excitement!